MAE 412 Design of Thermal Systems
Design Project Description
The Srinath Ekkad Steam Electric Power Plant is under design to provide700 MW net output additional generating capacity for the Duke Energy system. You are the design team responsible for the condenser in the turbine cycle and the components in the circulating water system that provides cold water to the condenser.
The circulating water system components include three pumps in parallel to provide the design flow, and the associated piping and valves to supply the water to the condenser. The water is drawn from a captive lake and is returned to the lake.
The design point for the project is full load (735 MW generator output) when the lake temperature is 85oF. The team responsible for the turbine cycle has already established that the efficiency of the unit, described as turbine cycle gross heat rate and based on the generator output, is 9000 Btu/kWh. The design circulating water system flow is 273,000 gpm. However, the three pumps have already been purchased and may or may not be able to meet the design flow rate.
Your input to the project will consist of the following three parts:
- Condenser design: analysis of four design options and their impact on condenser pressure.
- Circulating water system design: model the piping, valves, condenser, and pumps to find the expected flow rates and pump discharge pressures for all condenser tubing options under consideration.
- Cost-optimization: analyze the four tubing options to determine the least-cost alternative to recommend to the project.
- Condenser Design
The 'footprint' under the steam turbine requires that the condenser tubes be 50 feet long. The water goes through one tube pass, then makes a u-turn and returns through a second set of tubes. The active volume in the condenser for each set of tubes is 10 feet wide and 15 feet high. Assume the convective heat transfer coefficient, hD avg, for the condensing steam is 7500 W/m2-K for 7/8" tubing and 7250 W/m2-K for 1" tubing. Your suppliers can supply you with the following tube options:
Admiralty 1" OD or 7/8" OD: 18 BWG
Stainless Steel 304 1" OD or 7/8" OD: 22 BWG
- Using a rule of thumb that the ligament between tubes (minimum distance between holes in the tubesheet) is one-fourth of the tube outer diameter, create a table of expected condenser pressures for the four tubing options.
- Report the number of tubes required versus tubing option.
- Compare your overall heat transfer coefficients U with the HEI-predicted U's for the four cases..
- Calculate an inlet temperature correction curve for the overall heat transfer coefficient and compare it graphically with the HEI curve over a temperature range of 50oF to 90o
- Circulating Water System Design
Model the CWS using the given piping drawings and pump performance curves. (The condenser discharge butterfly valves are closed to provide a K = 10 to throttle the flow and raise the pressure in the discharge waterboxes. Otherwise the strong vacuum created by the siphon effect will cause dissolved gases to come out of solution and build up a gas bubble which will uncover some of the condenser tubes, thereby reducing the heat transfer surface.)
- Find the CWS flow rate for each of the condenser tubing options.
- Find the pump discharge pressure for each of the tubing options.
- If Pump C is taken out of service, find the CWS flow rate for 1" OD BWG 18 Admiralty tubing.
- If one side of the condenser is isolated by closing a pair of inlet and discharge butterfly valves in order to clean tubes while the unit is running, what will be the flow rate through the other half of the condenser? Calculate for the 1" OD BWG 18 Admiralty tubing option.
- Cost-Optimization and Selection of Tubing Material
Analyze the total cost of each tubing alternative. Write a report recommending the least total cost alternative and documenting your analysis.
Cost of tubing:
0.875 304SS - $1.48/ft
1.000 304SS - $1.70/ft
0.875 Admiralty - $6.31/ft
1.000 Admiralty - $6.65/ft
Installation cost: $20/tube
Interest: 5%
Inflation: 3%
Taxes: 1% of initial installed cost/yr
Insurance: 0.08% of installed cost/yr, inflated
Oper & Maint Cost: 1% of installed cost/yr,inflated
Salvage value: 5% of initial cost, inflated to end of life
Tubing life: 20 year Admiralty, 20 year SS 304
Maximum Capacity cost factor: 60 $/kW-yr (Industry jargon: "load penalty factor")
Energy cost factor: 50 $/MWh (Industry jargon: "heat rate penalty factor")
Operating time: equivalent full-load for 70% of the year (8760 hr/std year)
Attachments to be sent out:
- HEI Condenser Standards, selected pages
- Flow of Fluids, selected pages
- CWS piping diagrams - part of Description
- Pump performance curves
- Generator Output correction curve for condenser pressure
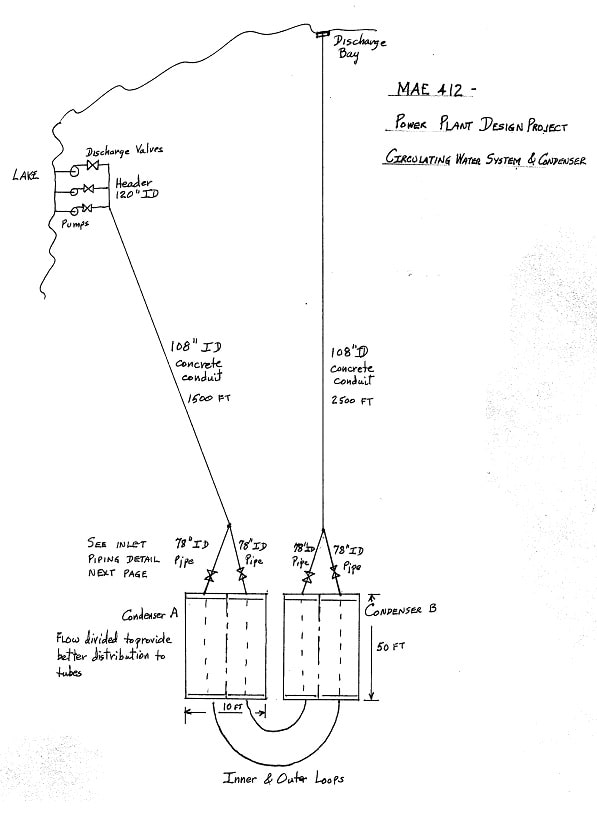
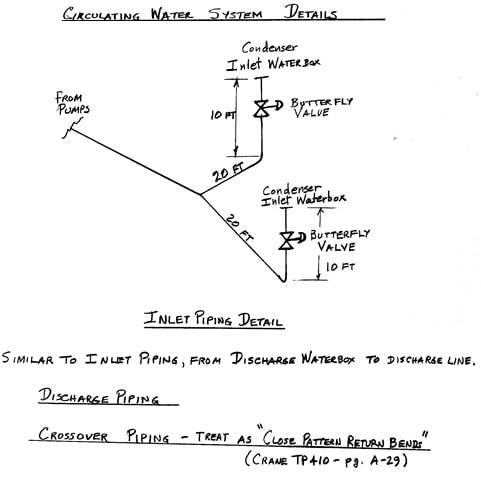