Model Making Assignment Help
In most cases architectural models are made to order in a workshop from designs already completed. Independent model makers are usually to be found in all larger towns, with well-equipped workshops in which commissions can be carried out to schedule by teams of craftsmen. In Europe model- making workshops attached to and serving only one particular architectural office are rare. Architects, indeed, do make their own models, but generally under primitive conditions. In the USA, where model- making, from preliminary space checks accompanying the first sketch to illustrating final details, has become a more important part of the design process, the combined architectural office/ model- workshop is more common.
For execution, first, the architect lays his plans before the model-maker and explains the object of the required model. The appearance in terms of type, scale, colour treatment and, of Assignment, the completion date and cost of the model are discussed. After this the programme is worked out. Before construction can start, appropriate drawings must be prepared. The architects design drawings are usually to a different scale or too inaccurate for use in cutting out model parts. According to the construction system chosen, which will be exactly specified (e.g. whether the model is to be transparent or the floors slotted, or how the joints are to be formed), a design variant of the architects plans is evolved especially for making the model. For this very exact drawings will be necessary, which must show an identical congruence of heights, widths and axes, so that all the different parts fit to the nearest millimeter.
The elevations, base board and core of the building can be tackled separately. Colour treatment and the assembly and fitting of the buildings component parts are also independent activities, undertaken either consecutively or in parallel.
Plaster models
The technique of making architectural models entirely in plaster is very old, but it is seldom learnt by model-makers today, being only used for special purposes. For example, participants in architectural competitions often obtain ready-made baseboards which include models of the surrounding buildings which are generally reproduced cast in plaster. For the design models built on this plaster base, architects and model-makers chiefly use acrylic sheet, paper or wood, and not plaster.
Plaster is primarily an outstanding material for casting, adaptable to any desired form. For casting sharp-edged slabs or blocks it is best to use shuttering of timber, acrylic sheet or plywood strips, disposed on a glass or cardboard base.
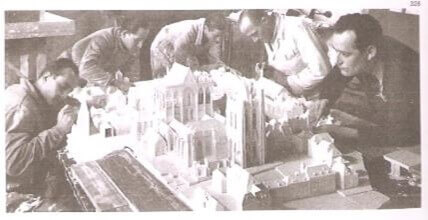
Model Making Assignment Help By Online Tutoring and Guided Sessions from AssignmentHelp.Net
These framing elements can be held firm with the hand until the plaster is set.
Foam-plastic models
In the large model-making workshops, the rationalization of time and labour has been mainly achieved through improved tools and processing machines. Architects and students on the other hand, who build their own models, save considerably by using low cost and time-saving materials. Foam-plastics undoubtedly head the list of these low cost materials. They are composed of the most varied base materials (preferably polystyrene, polyurethane and phenol basis), which, by means of added gases or gases formed during the manufacturing process, have been expanded into foams or other cell structures before solidifying through chemical interlacing, jellying or chilling.
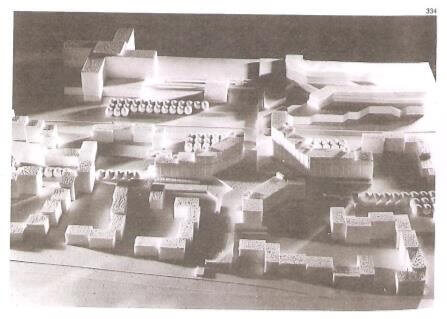
The surface structure is an important aspect in the choice of a specific foam plastic. As with wood and cork, too coarsepored surfaces distort the scale. For this reason, coarsestructured foam plastics are only used for mass models or fillings (which are then covered with other materials), while for detailed representations, fine structured sheets are preferable. Care must be taken by the application of adhesives. Not all adhesives are compatible with foam plastics. Some solvents decompose the material.
Paper, pasteboard and wood models
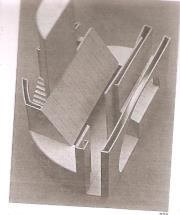
Paper is easily folded, rolled, bent, cut and stuck, being suitable for almost every conceivable three- dimensional form. The architect, who wants his models sharpedged and white, will turn to fashionplate board. The student, who does not have to account for his working time on study models, will find in paper and card his cheapest model-making materials.
Making models with paper is simple. All external surfaces can be made in accord with the design, the faade features being drawn and, in certain parts of the surface, cut out. All bend lines are previously scored with a needle to make the angles sharp. When assembling, in order to avoid clumsy joints, narrow folds of paper are left along the edges for sticking. These enable one to dispense with all-pupose glues with their usually untidy-looking lumps and trickles.
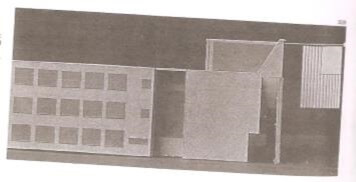
Pasteboard models also belong to the group involving cheap materials and long working hours. Being composed of flat surfaces, pasteboard can only be used for cube-shaped buildings. White pasteboard gives the neatest results, but its cut edges must be very cleanly squared. Cutting is done with knives, their blades as thin and sharp as possible to avoid widening the cut surface.
Models made entirely of wood are uncommon. Although wood is easy to work, its use is generally confines to large-scale construction models, buildings in town-planning models, accessories and built-in fillet or dowel sections as for structural cores. Distortion caused by damp can completely alter accurately made wooden models.
Acrylic sheet models
While paper, pasteboard and wood models are often simply made to illustrate a formal composition of solid wall and roof elements with window openings unglazed, when needed a more true-to-life image will often be obtained by building glass surfaces into the model. Acrylic sheets are the best but most expensive materials for this, and preferable to fragile glass. Acrylic responds to accurate workmanship, can be neatly stuck and coloured and is permanently resistant to the effects of damp and temperature.
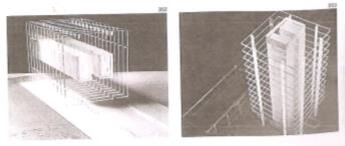
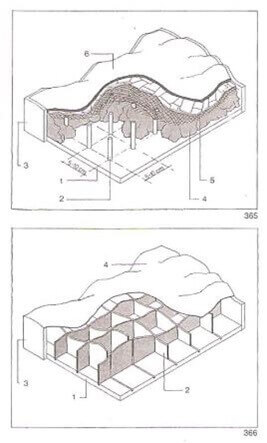
Baseboards
Making the site is one of the first and principal jobs; it begins with a solid baseboard, whether the ground to be represented shows contours or not. For this bottom layer, plywood or chipboard sheets are preferable to hardboard, which is too inelastic and does not take nails well. The starting point for the site is a survey plan in duplicate; for setting ou the contours and tracing roads, boundaries and building locations.
The technique of representing ground contours in plaster is frequently regarded as out of date, although it takes little time, once mastered. At intervals of 5 to 10 cms wood dowel pegs are placed on the plan which is stuck onto the baseboard- their tops conforming to the lie of the land. These form the supporting framework for a covering of wire mesh and plaster, the latter built up in layers with strips of sacking or bandage and smoothed with a palette knife. The ground heights are worked out in detail afterwards.
Bibliography
- Engineering drawing and graphics- K. Venugopal
- Principles of design in architecture- K.W. Smithies
- Colour for architecture- Porterard Mikellides
- Architectural Models- Rolf Janke
- Design fundamentals- C.J. Feldsted
- Design fundamentals- Robert Gillam Scott
- Carpentry and joinery for building craft students- Peter Brett
- Design concepts basic guidebook- Gail Lynn Harturgsen
- Design methods- John Chris Jones
- Logic & Design-Krome Barratt