Lab 106 static and kinetic frictions
- Lab 106(2): Static and Kinetic Frictions
- Introduction
Whenever the surface of one object slides over another surface, friction results. The frictional force is always parallel to the action of these surfaces, opposite of the motion relative to the other. Suppose a system exists where a block is at rest on a table. An applied force is created. Static frictional force (fs), increases, balancing out the applied force until the object starts sliding. At the moment right before the object starts sliding, the maximum fs was reached. The relationship between the fsmax and the normal force, FN, is as followed: fsmax = μsFN.
Once an object begins sliding, kinetic friction takes over static friction. The kinetic, or sliding friction between two surfaces is given by: fk = μkFN. If sliding takes place at a constant speed, Newton’s First Law applies to the system. The coefficient of kinetic friction is always smaller than the coefficient of static friction. It requires a greater force to start an object moving than it takes to maintain movement.
- Experimental Procedure
Part I. Find Static and Kinetic Friction Coefficients between wooden cart and friction apparatus under a horizontal condition.
- The USB cable of the 850 Universal Interface was connected to a USB port on the computer.
- The AC adapter power cord was connected to an electrical outlet under the lab table.
- The computer program to be used for the lab was opened up.
- The mass of the wooden cart was measured to be 85.09 grams or 0.08509 kg.
- The force sensor was zeroed.
- The wooden cart was put on the friction apparatus. The top of the pulley was observed to be the same height as the hook of the cart, threaded over a wheel and onto the table.
- The record button in the program was pressed.
- The motion sensor was slowly pulled until the cart started to move. We then continued to pull the cart at constant velocity.
- After obtaining data, we pressed the stop button and clicked to the Analysis 1 page.
- Data was selected for use using the select visible data tool. Looking at the generated chart, we approximated for coefficients of kinetic and static friction.
- We clicked to the page Analysis 2 and entered the coefficients found in step 10 along with the calculated normal force for each trial.
- Steps 5-11 were repeated for 5 trials, with 5 different normal forces for the friction tray.
- In the page Analysis 2, there were data points formed on a Ff v. FN graph for every trial. Two points were generated for each trial, one point for the kinetic friction, and one point for the static friction. At the end of 5 trials, lines of fit were generated with the curve fit tool for the points of static friction and kinetic friction separately.
Part II. Wooden Cart Moving Up and Inclined Plane
- The critical angle (15.6o) for the wooden cart to be on the verge of sliding down an inclined plane was experimentally determined.
- The friction apparatus was inclined to an angle smaller than the critical angle.
- Using the coefficients of static and kinetic friction found in part 1, the theoretical values of the maximum static and kinetic friction forces were when a cart was moved up the incline was found.
- The friction apparatus was set up the same incline angle as step 1 to experimentally measure the maximum static and kinetic friction forces.
- The procedures in Part 1 were used to perform measurements. The percent difference between experimental and calculated values of forces were found.
- Results (Data and Conclusion)
4.1 Experimental Data
Part 1
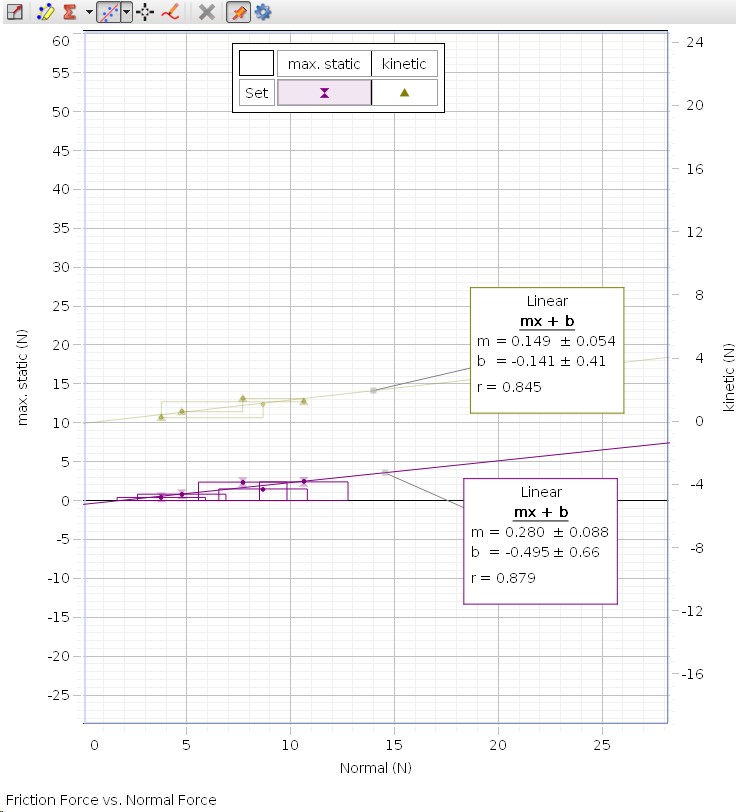
Normal Force (FN) |
Maximum Static Friction (Ffs) |
Maximum Kinetic Friction (Ffk) |
8.673882 N |
1.49 N |
1.08 N |
3.773 N |
0.4 N |
0.22 N |
10.633 N |
2.4 N |
1.23 N |
7.6938 N |
2.37 N |
1.44 N |
4.7538 N |
0.82 N |
0.6 N |
Part 2 ![]() (Track inclined at 30o) | ||
Normal Force (FN) |
Maximum Static Friction (Ffs) |
Maximum Kinetic Friction (Ffk) |
7.51 N |
7.94 N |
7.01 N |
3.27 N |
2.25 N |
1.82 N |
9.21 N |
8.85 N |
8.41 N |
6.66 N |
6.02 N |
5.43 N |
4.12 N |
3.8 N |
3.32 N |
Theoretical values of force for 10o
Normal Force (FN) in Newtons |
Maximum Static Friction (Ffs) |
Maximum Kinetic Friction (Ffk) |
8.54 N |
2.41 N |
1.28 N |
3.72 N |
1.05 N |
0.55 N |
10.5 N |
2.96 N |
1.56 N |
7.58 N |
2.14 N |
1.13 N |
4. 68 N |
1.32 N |
0.7 N |
The data charts recorded by the program and observed for frictional coefficients are as seen below:
Part 1
Part 2
4.2 Calculations
For part 1, since the track was horizontal, FN = -Fg. Fg or weight was calculated as followed: Fg = mg. The mass was different for each trial, but the acceleration was always the same, at 9.8 m/s2. For trial 1, FN = (0.8 kg (800 grams of weight in cart) + 0.08509 kg (mass of cart) )x(9.8 m/s2) = 8.673882 N.
For part 2, since the track was inclined, the normal force was equal to the negative vertical component of Fg, so FN = Fgcos30o. Trial 1 part 2 sample calculation: FN = (8.673882 N)cos30o = 7.51
Calculations for Critical Angle: FBD below:
Looking at the FBD, one can see that the calculations are as followed:
x |
y |
ΣFx = max Fg = mg = (0.0809 kg)(9.8 m/s2) = 0.8339 N μs = 0.28 (from Part 1 graph) Fgx – Ffs = max Fgsinθ - Ffs = 0 (0.8339 N)sinθ - (0.28)FN = 0 |
ΣFy = may Fg = 0.8339 N FN – Fgy = may FN – Fgcosθ = 0 FN – (0.8339 N)cosθ = 0 FN = (0.8339 N)cosθ |
I can then take the x side equation (0.8339 N)sinθ - (0.28)FN = 0 and substitute with FN from the y side equation, FN = (0.8339 N)cosθ.
(0.8339 N)sinθ - (0.28)FN = 0
(0.8339 N)sinθ - (0.28) (0.8339 N)cosθ = 0
(0.8339 N)sinθ = (0.28) (0.8339 N)cosθ
[(0.8339 N)sinθ = (0.233492 N)cosθ] x 1/sinθ
0.8339 = (0.233492 N)cotθ
0.8339 = (0.233492 N)/tanθ
0.8339 tanθ = 0.233492 N
tanθ = 0.28
θ = 15.6o
The next part of the experiment required that we choose an incline angle smaller than the critical angle and determine the applied force needed to make the wooden cart be on the verge of moving up the inclined plane, and the force that keeps the cart moving at constant speed. Incidentally, we chose an angle of 30o, much larger than 15.6o, so our results were very off. But had we theoretically chosen an angle of 10o, sample calculations would have been as followed:
2 things to find:
- FA when Ffsmax
- FA when Ffk
FBD:
FA when Ffsmax (No weights on cart) | |
x |
y |
ΣFx = max μs = 0.28 (from Part 1 graph) Fg = mg = (masses + 0.0809 kg)(9.8 m/s2) FA – (Fgx + Ffsmax) = 0 FA – ((Fg)(sin10o) + (0.28)(Fg)(cos10o)) = 0 FA = Fg(sin10o + (0.28)(cos10o)) FA = Fg(0.4494) |
ΣFy = may FN – Fgy = 0 |
FA when Ffk (No weights on cart) | |
x |
y |
ΣFx = max μk = 0.149 (from Part 1 graph) Fg = mg = (masses + 0.0809 kg)(9.8 m/s2) FA – (Fgx + Ffk) = 0 FA – ((Fg)(sin10o) + (0.149)(Fg)(cos10o)) = 0 FA = Fg(sin10o + (0.149)(cos10o)) FA = Fg(0.3204) |
ΣFy = may FN – Fgy = 0 |
In addition to that, we were also asked to find the theoretical values of the maximum kinetic and static friction forces when you move the cart up the inclined plane. As can be seen from the sample calculations above, the Ffsmax = (0.28)(Fg)(cos10o) = 0.278Fg, and Ffk = (0.149)(Fg)(cos10o) = 0.147Fg. I then derived the values for the theoretical data chart from these calculations.
4.3 Error Analysis
There was significant error in this experiment. Because for part two we performed the experiment at a much higher angle (30o) than the critical angle at 15.6o, the percent error is expected to overshoot 100% in some cases. Besides that, there could have been error in reading the data off the program graphs, technical error in the data collection tools, error in the type of cart used, error in pulling the pulley, etc.
Sample error calculations: (for trial 1)
Theoretical/True Values for FN, Ffs and Ffk:
FN = 8.54 N
Ffs = 2.41 N
Ffk = 1.28 N
Experimental Values for FN, Ffs and Ffk:
FN = 7.51 N
Ffs = 7.94 N
Ffk = 7.01 N
Trial 1, FN error
Eabs = observed value – true value
Eabs = 7.51 N – 8.54 N = -1.03 N
7.51 N ± 1.03 N
Erel = Eabs /true value
Erel = 1.03 N /8.54 N
Erel = 12%
Trial 1, Ffs error
Eabs = observed value – true value
Eabs = 7.94 N – 2.41 N = 5.53 N
7.94 N ± 5.53 N
Erel = Eabs /true value
Erel = 5.53 N /2.41 N
Erel = 229% error
Trial 1, Ffk error
Eabs = observed value – true value
Eabs = 7.01 N – 1.28 N = 5.73 N
7.01 N ± 5.73 N
Erel = Eabs /true value
Erel = 5.73 N /1.28 N
Erel = 448% error
Error Table for Part 2:
Normal Force (FN) |
Maximum Static Friction (Ffs) |
Maximum Kinetic Friction (Ffk) |
12.1% |
229% |
448% |
12.1% |
114% |
231% |
12.3% |
199% |
439% |
12.1% |
181% |
381% |
12.0% |
188% |
374% |
- Discussion
The prediction of force values was not close at all to the experimental result. My group did not perform the lab correctly, and used an angle much too large for results to be accurate. Percent error ranged from 12% to over 400%, as expected since the difference in theoretical calculations and the actual experiment was about 20 degrees. Had we performed the experiment with an angle beneath the critical angle of 15.6o, the results probably would have been a lot more accurate. The error was significant, and to prevent this same problem next time and improve upon these results, I would suggest more closely monitoring the experimental procedure and checking twice to make sure all experimental goals are met.
Besides that, sources of error could have included errors of reading the degree measurements on the friction apparatus, error in manually recording and measuring data, error in setting up the experiment, using the wrong force cart, failing to pull the cart in an appropriate manner for data collection, forgetting to hit the zero button on the force sensor, among other things. Systematic error could have occurred because supposing the friction apparatus or the table was tilted or there was some other inconsistency not accounted for, results could have been slightly skewed up or down. Random errors could have occurred as well. Some trials were not performed as carefully as others, and it was difficult to gradually increase the amount of force until the object started moving, especially at the lower weights. For that reason, there could have been an increased error with results at lower weights.
There were 3 Pasco trays with surfaces of cork, felt and plastic. However, we only performed the experiment with one tray. Had we experimented with all three, it is likely that the order for the coefficients of friction would have been cork, felt, and then plastic. It has been proven through other experimentation that cork usually has the highest coefficient of friction followed by felt and plastic.
Looking at the Force v. time graph, during time A, the object has increasing static frictional force, and at point B, the maximum static frictional force is reached. From time A to B, the object is not yet moving, since the applied force has not overtaken the frictional force. After B, C occurs, when the object starts moving and the coefficient of friction becomes kinetic, less than the maximum static friction coefficient. At D, the object has settled into moving at a constant speed, and as shown, the applied force is constant as well.
The normal force on the bottom surface did not affect the coefficient of static and kinetic frictions. Coefficient of static and kinetic friction depends entirely on the types of surfaces being rubbed together, not the weight of rubbing them together, though the frictional force is impacted by the normal force, as shown in the equations Ffs = μsFN and Ffk = μkFN.
The values of the coefficients of static and kinetic friction have an observable relationship. Static friction increases up to a maximum force before movement. Maximum coefficient of static friction is always greater than kinetic friction of a constant speed.
- Conclusion
As this lab is concluded, I now know how to test for the static and kinetic frictional forces using a force sensor. I also know how to measure the coefficients of static and kinetic friction between surfaces and how to calculate and analyze forces using a FBD. However, we probably failed some objectives of the lab in performing the 2nd part of the experiment incorrectly. But since I performed the theoretical calculations and understand how they work, I have come through with an understanding about how to accurately perform the lab, were it to be done again and of the underlying concepts the lab tries to teach. I would be sure to look more closely at the procedure and take precautionary measures that nothing is missed.
For this lab, we performed 5 trials each for Part 1 and 2 of the lab to observe the relationship between static and kinetic frictional forces. Using graphs of frictional force v. normal force, we were able to derive static and kinetic coefficients, since f = μFN, and the relationship carries through on a graph, where the coefficient represents the slope of the graph, understanding that linear plots take the format y = mx + b. The intercepts were negligible, since the graphs were all approximated to cross the axises at the origin. To solve for various forces and angles, I was able to use Newton’s 2nd Law, which states that F = ma. By dividing up the forces that act on a system into vertical and horizontal components, I was able to solve for these variables and determine the relationship between the coefficients of friction, that kinetic friction under constant speed is always less than the maximum static friction coefficient.