Inventory Management Assignment Help
What is Inventory?
Inventory refers to the assets of the company which consists of raw materials, work in progress and finished goods that are ready for the sale or will be ready for the sale. It is the goods and material company holds for the ultimate purpose, resale. It is held by the organization to support production, repairs, maintenance or for sale. It is the major part of the assets of the business because inventory turnover represents one of the primary sources of the revenue generation. Inventory can also be on consignment, which is an arrangement when a company has its goods at third-party locations with ownership interest retained until goods are sold. When the inventory is sold, the carrying cost goes to the cost of goods sold on the income statement.
Organization must take care about the inventory, because at the end of the accounting period, it is one of the major factors of deciding profit and loss for the organization.
Inventory Management
Managing inventory and stock of the company is known as Inventory Management. It is one of the elements of Supply Chain Management and includes all aspects related to inventory for instance, controlling or overseeing ordering inventory, storage of inventory and controlling the amount of product for sale. The scope of inventory management concerns the balance between replenishment lead time, carrying costs of inventory, asset management, inventory forecasting, inventory valuation, inventory visibility, future inventory price forecasting, physical inventory, available physical space, quality management, replenishment, returns and defective goods, and demand forecasting.
This entire requirement must be balanced to meet the optimal inventory level. It would include monitoring of materials moved into the stockroom and out of stockrooms.
Reasons for keeping stock
a) Time- It is important for the producer to have certain amount of inventory because there is generally a big time difference between giving order for the inventory and receiving it. So, organization must make sure about the time when it requires the inventory so that the production process doesn’t get stopped.
b) Seasonal Demand- Demands varies periodically, but producer’s capacity is fixed. This can lead to stock accumulation; consider for example how goods consumed only in holidays can lead to accumulation of large stocks on the anticipation of future consumption.
c) Uncertainty- There is no certainty about the demand of the consumers. Their demand might get higher at a point of time, and to take the advantage of the increase in the demand of the customer, company must have enough stock of inventory to increase the level of production.
How to know the right amount of inventory to stock?
Company must have the right amount of inventory in the organization. It is crucial and a bad decision related to it may lead to incur in high cost. Company having fewer inventories than required will decrease the supply of the product and customer’s demands will not be fulfilled so they will go somewhere else. In a survey, when the business owners were asked how they decide the reordering item of the inventory, they replied with ‘previous month information.’
To calculate the right amount of inventory, previous month information should also be accurate and reliable else it might not produce the data management wants.
How to determine the right price?
Firms do not like to pay more than they should be. But lower prices aren’t good. They promise lower prices for higher amount of inventory purchased. But whether is it a good sign for the company to have larger amount of inventory to gain a small amount of discount. An inventory not only increases the cost but also increase the various costs related to inventory. More the inventory, more the carrying and storage cost.
Company can find the right amount of inventory which they should have by Economic Order Quantity. It calculates the order quantity which will be economical for you company. Formula,
EOQ = √2DK/H
D = Fixed Cost per year
K = Demand in units per year.
H = Carrying cost per unit per year.
When should a firm order inventory?
It is one of the major questions that prevail in an organization when to order inventory. EOQ helps firms in determining the quantity of inventory that should be maintained by the company but not the time of reordering of inventory.
To calculate the reorder point, firm should know about:
- Time, it takes to get your items picked.
- Time, it takes to get items packed.
- Lead time.
{` Reorder point = Lead Time X Avg. daily usage + Safety Stock Safety Stock = Emergency stock kept for the uncertainty. Safety Stock = [Maximum Daily Usage X Maximum Lead time (days)] – [Average daily usage X Average lead time (days)] `}
Inventory Management Assignment Help By Online Tutoring and Guided Sessions from AssignmentHelp.Net
Inventory Level Equations
- Reordering Level = Maximum Usage x Maximum Re order level period
- Maximum Level = Re-ordering level + Re - ordering quantity - (Minimum usage * minimum re - order period)
- Minimum Level = Re - ordering level - (Normal usage * Normal re - order period)
- Avg.Stock Level = (Maximum Level+Minimum Level)/2
Illustration:
{` Two components A & B are used as follows: Normal Usage 100 per week each Minimum Usage 80 per week each Maximum Usage 200 per week each Re-ordering quantity A- 2000 Re-ordered period A- 10 to 20 weeks For each component, calculate: Re-ordering level; (b) Minimum level; (c) Maximum level; (d) Average stock level `}
Solution
{` a) Reordering Level = 200 X 20 = 4000 units b) Minimum Level = 4000-(100 x 15) = 2500 Units c) Maximum Level = 4000 + 2000 – (80 x 10) = 5200 Units d) Average Stock Level = 5200 + 2500 / 2 = 7700/2 = 3850 Units `}
Inventory Accounting Methods: FIFO methods and LIFO Method
FIFO
FIFO method refers to first in, first out, meaning that the oldest inventories items are recorded as sold first but do not necessarily mean that the exact oldest physical object has been tracked and sold. It is done on the assumption that the goods are used in the order they are purchased.
Advantages of FIFO Method
- a) It confirms to the actual flow of inventory items.
- b) It is inexpensive comparing to other methods.
- c) Management will find hard in manipulating the data.
- d) Ending Inventories are closed to current costs.
Disadvantages of FIFO Method
- a) In this method, actual cost of each transaction is not identified rather an assumption is made.
- b) If the firm buys in bulk to get a discount then benefit under this method will not be flow through to profit until older units are sold.
- c) Higher revenue leads to higher tax payments.
Process
Let’s understand the process by an illustration.

First Step: - Make FIFO Periodic. Write the total purchases made against the total sales made.
{` Units Available for Sales = 400 + 250 + 200 = 850 (Purchases) Units Sold = 300 + 240 = 540 (Sales) Units in Ending Inventory = 850 - 540 = 310 `}
Second Step:- Make a table of Cost of Goods Sold.
Date | Unit | Cost | Total |
---|---|---|---|
1-Apr | 400 | 75 | 30,000 |
12-Apr | 140 | 67.2 | 9408 |
540 | 39408 | ||
Ending Inventory | |||
110 * 67.2 | 7392 | ||
200 * 83 | 16600 | ||
310 * 77.39 | 23992 |
Third Step: - Prepare FIFO Perpetual
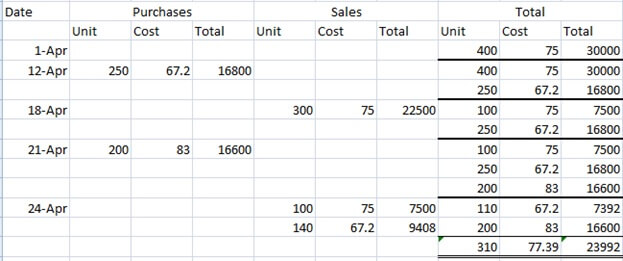
First of all, write the balance that is brought down in the total column. Then there is a purchase made on April 12, so write the unit, cost and total of that purchase respectively and add in the total column with the carry forward balance. Now there is a sale on 18 April, so we need to sale 300 units. And the price charged will be 75 because in this method, we will use the inventory in order we are having, so we carried the balance of previous month so we will use that inventory first and if still balance remains, then we will go forward with the purchases made. This will happen till the entry made and the balance of the unit and total must be equal to the balance of cost of goods sold ending inventory.
LIFO Method
It is very common technique that is used in the process of valuing the inventory. It is opposite of the FIFO method because it assumes that goods which made later to the inventory are sold first and those which are manufacturer earlier are sold last.
Advantages of LIFO method
- a) It matches current costs with the current revenue.
- b) LIFO method doesn’t increase the taxable income with the increase in revenue.
- c) Less tax means more revenue of the company.
Disadvantages of LIFO method
- Value of inventories in the balance sheet is unrealistic as it doesn’t reflect current market conditions.
- Comparison of similar job’s cost is difficult.
- LIFO yields lowest net income and therefore there are reduced earnings.
- Under this method, closing stock is not measured at recent price.
Process
- In LIFO method also, first you need to calculate LIFO periodic. LIFO periodic is calculated by subtracting total inventory available for sales by inventory sold.
- In the second step, cost of goods sold will be calculated. Unlike FIFO method, inventory at the end will be given preference over first. So, calculation will start from the last inventory units purchased.
- Remaining balance of inventory will be multiplied by the respective cost and total units of the ending inventory will be ascertained.
- Now we will prepare LIFO perpetual and in this first of all balance carried down will be transferred to balance column. Now purchase will be written in the purchase column as well as total column. And when it comes to sales, sales will be written on the sales column and the price charged will be from the recent purchase made.
For example-
There is a balance of units 4000 @ $5 on April 1, 2017 and on April 5, 2017 purchases of units 1000 @ $7 is made. There is a sale of 300 units. So 300 will be deducted from the last purchase of (1000 units) not 4000 units. And in the end of the month, the balance must match to the ending inventory of the cost of goods sold.
Gross Profit Method
It is a method which is used to calculate the ending inventory and cost of goods sold of a period on the basis of historical gross profit of the business. It assumes that gross profit remains stable during the period.
Process
- Calculation of the cost of goods available for sale by adding net purchases, related cost of purchases in cost of beginning inventory.
- Determine the gross profit ratio. Gross Profit Ratio = Gross Profit / Sales.
- Multiply Sales made during the year by gross profit ratio to obtain estimated cost of goods sold.
- Calculate the cost of ending inventory by subtracting estimated cost of goods sold with cost of goods sold.
For example-
Cost of Beginning Inventory - $25000
Net Purchase at Cost - $480,000
Freight Cost on Purchases- $20,000
Cost of Goods Available for Sale = 5,25,000
Less: Estimated Cost of Goods Sold:
(Sales $700,000
Less: Estimated Gross Profit 40% - 280,000)
Estimated cost of goods sold- 420,000
Estimated cost of inventory = 525,000 – 420,000 = 105,000