Sample Chemistry Course on Corrosion
Introduction
Physio-chemical interaction between a metal and its environment which results in changes in the properties of the metal and which may often lead to impairment of the function of the metal, the environment, or the technical system of which these form a part is called corrosion (ISO 8044-1986).
Or in general we can say, loss of electrons of metal reacting with water and oxygen. According to U.S. FHA study on Corrosion Costs and Preventive Strategies in 2002 (on direct costs associated with metallic corrosion in every U.S. industry sector), for 1998 the estimated total annual direct cost of corrosion was approximately $276 billion (which was around 3.1% of US GDP). Economic damage caused by electrochemical corrosion itself is between $8 billion and $128 billion per year in the US alone, degrading structures, machines and containers. For example, rust is one of the most common causes of bridge accidents. Rust has a much higher volume than the originating mass of iron, its build-up causes failure by forcing apart adjacent parts. Thus there is a need to control corrosion to prevent this damage both on economic and safety fronts.
Fundamentals Of Corrosion
Corrosion is caused by the flow of electric current from areas of a metal surface through a conducting solution (or environment). Eating away of metal due to this electric current occurs at areas which are called anodes, where the electricity leaves the metal, entering the environment exposed to it.
Bonds between metal ions contain a lot of free potential energy, which has a tendency to be released through the process of corrosion (i.e. oxidation) converting the metal to its natural state. This difference in the binding energies between the metal atoms is the driving potential towards the oxidation of metal atoms, resulting in the loss of one or more electrons and the production of the ionic form of the metal.
Corrosion occurs in the presence of moisture. For example when iron is exposed to moist air, it reacts with oxygen to form rust, the steps are:
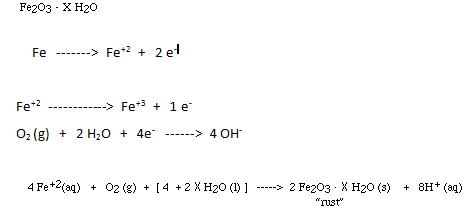
It is possible that the rust forms at some distance away from the actual pitting or erosion of iron shown in the figure. This occurs as the electrons produced due to the initial oxidation of iron can be conducted through the metal and the iron ions can diffuse through the water layer to another point on the metal surface where oxygen is available. Electrochemical cell results in the process in which iron serves as anode, oxygen as cathode and aqueous solution of ions serving as a 'salt bridge' as shown below.
Measures To Prevent And Control Corrosion:
For corrosion to occur, an anode, a cathode and electrolyte are essential as shown in the corrosion triangle. If by any means linkage within this triangle is broken, corrosion can be controlled and prevented.
Basic methods of controlling corrosion and protection are:
- Selecting corrosion resistant materials w.r.t. our surroundings:
- Apart from the factors of cost, availability etc, corrosion resistance must be considered as a part of overall material selection process. Analysis from previous applications experience and corrosion testing data are used for material selection in specific locations of our system. Down to the basics, a metal less willing to oxidize in our conditions is the material we are looking for. A metal with higher standard electric potential for oxidation of hydrogen is preferred generally from the electromotive series.
- Corrosion inhibitors:
- They aid in modifying the environment around our system so as to prevent or slow corrosion down. Inhibitors retard corrosion by increasing polarization of anode and cathode and by increasing the electric resistance due to formation of a deposit on the surface of metal. Examples of corrosion control using inhibitors include, modifying structures to provide desired drainage, using inhibitors in power plants or engine cooling systems.
- Cathodic protection:
- The basics of this method lie in lowering the difference between potential of anode and cathode by supplying an electric current from outside source. Buried and structures in contact with water like pipelines, underground storage tanks etc are protected effectively using this method. Thus the natural electrochemical cell action is hampered by the use of cathodic protection method. There are 2 different ways in which current can be passed:
- Sacrificial anode method:
In this process, due to corrosion of an active metal like zinc, required electric is produced. This way the active metal is sacrificed by corroding itself and thus protecting the surface where we want to control corrosion. In order to quantify the use of this method, natural corrosion potential is used in the selection of metal to be sacrificed.
- Impressed current:
- In this method, we supply direct electric current from any other external source (sometimes even using a rectifier to convert AC to DC). An inert anode material is used in the process to complete the circuit.
- Using protective coatings:
- This method of corrosion control is the one which is most widely used around the world today. This when used with other methods of corrosion control explained above is very effective. There are 3 basic machanisms by which coatings enhance corrosion control:
- Barrier Protection:
- Moisture and other electrolytes become impermeable to the coating, thus a barrier is formed between surfaces which are susceptible to corrosion and the corrosion causing factors in the environment. Thus it slows down/stops the process of oxygen to approach the metal surface.
- Cathodic protection of steel:
- In some protective coatings there is present a high zinc particle (or any other active metal) loading. These particles are in electric contact with each other as well as with the underlying metal. Thus a sort of cathodic protection is created by the protective film.
- Inhibitive pigments:
- Protective coatings also function as inhibitors due to some pigments present in the coating. These pigments inhibit the corrosion at the interface of metal and coating, example red lead.
- Some other methods:
- Stable oxide layer forming metals:
- Due to formation of a stable oxide layer on the surface, further corrosion is prevented. Thus at first stage, metal which forms stable oxide layer must be selected, or/and oxidation resistance of some metals (generally alloys) has been improved by adding alloying elements like chromium, silicon, aluminium etc which on reaction with oxygen tend to form a stable oxide film which act as protective coating for metal when exposed to their service environments.
- Away from dry and moist environments:
- As seen from the triangle explained above, if efforts are made wherever possible to keep metal in dry and away from moist conditions, most forms of corrosion can be stopped.
REFERENCES:
[1] http://www.corrosionist.com/corrosion_control_methods.htm
[2] https://en.wikipedia.org/wiki/Corrosion
[3] http://corrosion-doctors.org/Principles/Theory.htm
[4] Corrosion and corrosion protection, Philip A. Schweitzer, 1989 second edition.
[5] Principles and prevention of corrosion, Denny A. Jones, 1996 second edition.
[6] Corrosion: Understanding the basics, J. R. Davis, 2000
[7] Corrosion Mechanisms, Florian Mansfeld, 1986
Chemistry Tutor | Science Tutor | Chemistry Help | Chemistry Homework Help | Organic Chemistry Help | Help With Chemistry | Online Chemistry Help | Free Chemistry Help | High School Chemistry Help | College Chemistry Help | General Chemistry Help | AP Chemistry Help | Help In Chemistry | Help With Chemistry Homework | Help With Chemistry Homework | Help With Chemistry Homework | Physical Chemistry Help | School Homework | Chemistry Experiments | Homework Help | Homework Assignment Help | Online Tutoring Services | Term Paper Help | Online Tutoring